Scientists Discover the ‘Superpower’ of Self-Healing Metals, Promising to Revolutionize the Market
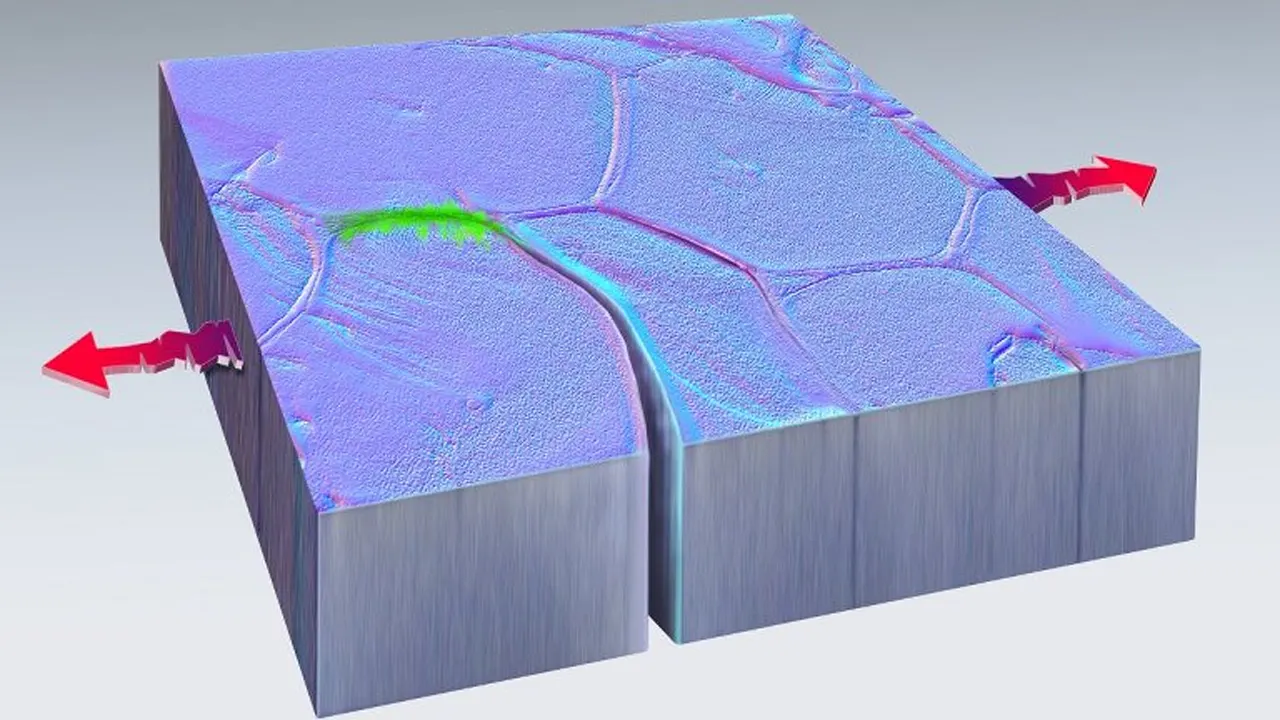
Self-healing metals have left the realm of science fiction and become a proven scientific reality. In 2023, researchers at Sandia National Laboratories and Texas A&M University successfully documented, for the first time, an extraordinary phenomenon: nanoscale platinum regenerating its own cracks without any external intervention. This discovery, published in the prestigious journal Nature, confirms decade-old theories and promises to revolutionize everything from airplane engines to bridges and electronic devices, fundamentally transforming how we design and maintain critical infrastructure.
The importance of this discovery transcends scientific curiosity. With global costs of metal corrosion and wear reaching $300 billion annually—equivalent to 3.4% of the world’s GDP—materials capable of self-repair represent a transformative solution to a gigantic economic problem. The technology already drives a $2.8 billion market in 2024, with explosive growth projections to $17.49 billion by 2033, fueled by applications ranging from NASA’s aerospace components to smart automotive coatings.
The Discovery That Changed Everything Began by Accident
The research at Sandia Laboratories, led by materials scientist Brad Boyce, did not initially aim to discover self-healing metals. The team was simply studying how cracks form and propagate in nanoscale platinum using a specialized transmission electron microscopy technique. The experiment involved repeatedly pulling on the ends of the metal 200 times per second, simulating the type of fatigue that eventually breaks machines and structures.
What happened next surprised the entire global scientific community. After about 40 minutes of observation, a nanometer-sized crack not only stopped growing—it literally welded itself shut, disappearing completely as if it “retraced its steps,” in Boyce’s words. The material had demonstrated an intrinsic and natural self-healing ability that challenged fundamental theories of materials engineering.
This experimental discovery confirmed a bold theory proposed ten years earlier by Michael Demkowicz, then at MIT and now at Texas A&M University. In 2013, based on sophisticated computational simulations, Demkowicz had predicted that, under certain specific conditions, metals should be able to weld cracks caused by wear and tear. His theory remained controversial until Sandia’s cameras captured the phenomenon in real-time.
How the Magic of Cold Welding Works
The mechanism behind metallic self-healing is fundamentally different from conventional self-healing materials, such as plastics with microcapsules. In metals, the process occurs through a phenomenon called “cold welding,” where atoms on clean metal surfaces cannot “distinguish” that they belong to different pieces when they come into close enough contact.
At the nanoscale, the diffusion barrier for a single metal atom is extremely low—approximately 1.0 electron-volt—allowing atomic diffusion to occur even with slight ambient thermal activation. The process is driven by grain boundary migration and surface rearrangement, where atoms spontaneously reorganize to minimize surface chemical energy.
Three metals have already demonstrated self-healing capabilities under controlled laboratory conditions:
- Platinum: The first metal observed with autonomous self-healing, functioning in samples ~40 nanometers thick, with complete healing observed in 40 minutes.
- Copper: Demonstrated crack deflection, retraction, and healing similar to platinum, confirming that the phenomenon is not exclusive to noble metals.
- Silver: Researchers at the Chinese Academy of Sciences confirmed in 2024 the autonomous self-healing in nanoscale silver, functioning from room temperature down to -100°C, repairing both nanopores and nanocracks.
The process is highly dependent on specific environmental conditions. Self-healing has only been observed in a vacuum environment, as the presence of oxygen and other atmospheric contaminants forms protective oxide layers that prevent the direct atomic contact necessary for cold welding. This limitation represents both a technical challenge and an opportunity for specific applications.
Practical Applications Are Already Transforming Critical Industries
Despite current limitations, multiple industries are already developing practical applications for self-healing technologies, some of which are already on the commercial market.
In the aerospace industry, NASA has developed SMASH (Shape Memory Alloy Self-Healing) technology, a patented aluminum matrix alloy with shape-memory alloy reinforcements that demonstrates 91.6% recovery of tensile strength. This technology received $275,000 in funding for the specific development of high-performance aircraft and applications in Mars missions, where structural repairs by human intervention are impossible.
The automotive sector already features real commercial products. BMW has integrated self-healing front grilles into the iX model, while the Korea Research Institute of Chemical Technology has developed coatings that self-repair in 30 minutes using solar radiation. These developments represent not only technical innovations but also practical solutions for reducing maintenance costs and improving the user experience.
The construction industry, which accounts for 34% of the self-healing materials market, is already implementing self-healing concrete in critical infrastructure. The Pacific Northwest National Laboratory has developed a specific self-healing cement for oil well casings, which repairs cracks in a few hours, avoiding repair costs that exceed $1.5 million per well.
In the electronics sector, researchers have developed flexible electrical conductors with liquid metal microdroplets capable of automatically restoring electrical conductivity when damaged, a critical technology for next-generation foldable devices and wearables.
Technical Limitations Define Future Challenges
Despite their revolutionary potential, self-healing metals face significant technical limitations that restrict immediate large-scale applications. The main barrier is environmental: the spontaneous self-healing process has only been convincingly demonstrated in a vacuum or an extremely clean atmosphere, limiting applications to space components, sealed electronics, or specialized equipment.
Scale represents another critical challenge. Effective self-healing has only been observed in materials with a thickness of less than 100 nanometers and nanocrystalline structures. As the material size increases, effectiveness decreases dramatically due to low atomic mobility and the need for elevated temperatures to activate diffusion mechanisms on a larger scale.
Material limitations also restrict applications. The process works best in pure metals with low surface energy and good atomic diffusivity, functioning preferentially in metals with a face-centered cubic (FCC) crystal structure. Complex alloys like commercial steels have not yet demonstrated convincing self-healing capabilities.
Economically, production costs remain 200-500% higher than conventional materials due to the need for nanometric processing, precise microstructural control, and specialized manufacturing techniques. However, total cost of ownership analyses indicate a payback period of 2-5 years depending on the application, due to the significant reduction in maintenance costs.
Global Research Ecosystem Drives Accelerated Innovation
The development of self-healing metals is driven by a highly funded global research ecosystem involving leading universities, national laboratories, and innovative companies worldwide. The U.S. National Science Foundation allocates $9.5 billion annually for materials research, with specific programs like DMREF (Designing Materials to Revolutionize and Engineer our Future) funding projects of $1.5-2 million focused on transformative materials.
Leading universities in materials science are spearheading fundamental research. Tsinghua University and Zhejiang University in China each have more than 100 elite researchers, while the Chinese Academy of Sciences has 379 top researchers—the largest concentration in the world. In the West, MIT, Stanford, and the universities of Cambridge and Oxford maintain robust research programs in self-healing materials.
Specialized startups are commercializing specific applications. CompPair in Switzerland develops solutions for composite structures with thermally activated smart prepregs for wind turbines and ship hulls. SAS Nanotechnology creates polymeric microcapsules for the on-demand release of anti-corrosion additives, while Basilisk in the Netherlands has been commercializing self-healing concrete since 2015.
Venture capital investment is substantial. The Material Impact fund raised $352 million specifically for materials science startups, while 55 startups in the field have received aggregate funding of $3.2 billion, with an average of $59 million per company, indicating significant market confidence in the technology’s commercial potential.
Environmental Sustainability Adds Strategic Value
In addition to direct economic benefits, self-healing metals offer substantial environmental advantages that align with increasingly stringent sustainability regulations. Extending the life cycle of structures and components reduces the need for new materials and prevents premature disposal, contributing to a more efficient circular economy.
Life cycle analyses show that 3D-printed self-healing materials can reduce primary energy demand by 26%, while self-healing geopolymer concrete has a lower global warming potential than conventional Portland cement. In the automotive sector, the implementation of self-healing technologies demonstrates a 28% reduction in global warming potential compared to conventional maintenance systems.
The prevention of catastrophic failures has significant direct environmental implications. Leaks in oil pipelines, structural failures in bridges, and building collapses generate not only gigantic economic costs but also lasting environmental impacts through contamination, resource waste, and the need for carbon-intensive reconstruction.
The Next Decade Promises Accelerated Transformation
The self-healing materials market is poised for explosive growth, with projections indicating an expansion from $2.8 billion in 2024 to $17.49 billion by 2033, representing a compound annual growth rate of 22.6%. The Asia-Pacific region leads with 30.15% of the market and the fastest growth at a 28.5% CAGR, driven by industrial expansion in China and Japan.
Three technological milestones will define the next decade. First, the development of self-healing processes functional in ambient atmosphere will eliminate the current limitation to a vacuum, expanding applications to conventional infrastructure. Second, the extension to larger scales through advanced processing techniques will enable structural applications in real engineering components. Third, integration with artificial intelligence for monitoring and selective activation of healing processes will create truly autonomous systems.
Transformative specific applications are already in development. In space exploration, self-healing structures will enable decades-long missions without maintenance in environments where human repair is impossible. In urban infrastructure, self-repairing bridges and buildings will reduce maintenance costs by 50% and eliminate catastrophic failures due to gradual deterioration.
Critical barriers require a coordinated solution. The standardization of testing and certification methods is essential for broad commercial adoption. The development of economically viable manufacturing processes will determine the speed of implementation. Educating the market about the total cost of ownership benefits will overcome initial resistance to premium costs.
Conclusion: A New Era of Materials Engineering
Self-healing metals represent more than an incremental innovation—they usher in a paradigm shift in how we conceive, design, and maintain material systems. The accidental discovery at Sandia Laboratories confirmed that materials possess intrinsic capabilities far beyond what we have traditionally assumed, opening up design possibilities previously confined to science fiction.
The convergence of scientific advances, massive investment, and market demand is accelerating the transition from laboratory curiosity to transformative commercial applications. Although current technical limitations restrict immediate implementation, the long-term potential justifies the substantial investments being directed toward this area.
The next decade will be decisive in determining whether self-healing metals will fulfill their revolutionary promises or remain a specialized technological niche. The evidence points to accelerated transformation: markets projected in the tens of billions, critical applications already in development, and solid scientific foundations established through rigorous experimental validation.
For engineers, architects, and designers, the message is clear: materials that heal themselves are no longer science fiction, but an emerging reality that will redefine design possibilities and maintenance strategies. Self-healing infrastructure promises safer, more efficient, and more sustainable cities—a vision that is rapidly becoming a tangible reality.
About the Author
0 Comments